3 min read
Debunking Top Myths: The Truth About Switching Maintenance Tracking Systems
Veryon : Sep 17, 2024 8:00:00 AM
Change is challenging! Are you letting fear hold you back from the best in technology for your aviation-based business? Whether you're using outdated software due to familiarity or because you're harboring reservations about switching to a new platform, now more than ever, it's critical that aviation companies look at their current systems to determine if they are performing at the level needed for optimum safety and performance.
Fear is often the underlying cause of why users stay with their existing tracking system, even if that current solution isn't working anymore.
Myth: A break in continual compatibility will cause challenge.
Fear: Users worry that integrating new systems with existing ones might lead to compatibility issues, potentially affecting data migration and tracking processes. With a variety of platforms using unique methods for task execution, initial compatibility concerns are understandable.
Debunked: Modern maintenance tracking systems are built with interoperability in mind. They often feature data mapping and integration tools designed to bridge compatibility gaps. Well-supported systems come with robust customer support and development teams that can address specific integration challenges.
Kim Watne: "You do have to be prepared to look at what you had and what you're getting into because your screens will look different, which can be confusing sometimes. I know when we changed maintenance tracking systems, that was one of the biggest things. But you just learn to train your brain to see things differently."
Complicated Transition Process
Myth: The transition process upon going live will be complicated and problematic.
Fear: Users often fear that data may not transfer correctly, and the transition process will be cumbersome. They might be concerned about having to run the legacy system alongside the new solution for an extended period or face difficulties with a complete and immediate switch.
Debunked: Transition strategies vary, and each approach has its advantages. While one option involves running the legacy system alongside the new solution for an extended period, users can also opt for a complete and immediate switch to the new system, forcing them to quickly adapt to the new platform.
Kim Watne: "When we went from our old maintenance tracking to our new tracking system, I ran a report, I turned off the old system, and I never went back. For me, that was the easiest way and simplest because I didn't have to worry about updating two systems."
Impact On Aircraft Value
Myth: Switching systems will devalue the aircraft.
Fear: There's a belief that changing systems might negatively impact the value of the aircraft. Users worry that the new system could affect the perceived value or create issues with documentation.
Debunked: Complete, well-documented, and accurate records that show prompt responses to Airworthiness Directives and other maintenance needs can enhance aircraft value rather than the other way around. If a user has been relying on an ineffective tracking system, the data may already be unusable, or the software may no longer be suitable for its intended purpose, which could negatively impact the value of the aircraft.
Kim Watne: "I think a well-documented aircraft does increase the value of your aircraft. I have seen aircraft being sold where the cockpit is full of aircraft records that go with the aircraft. I have seen them without it, and there's a difference in the price."
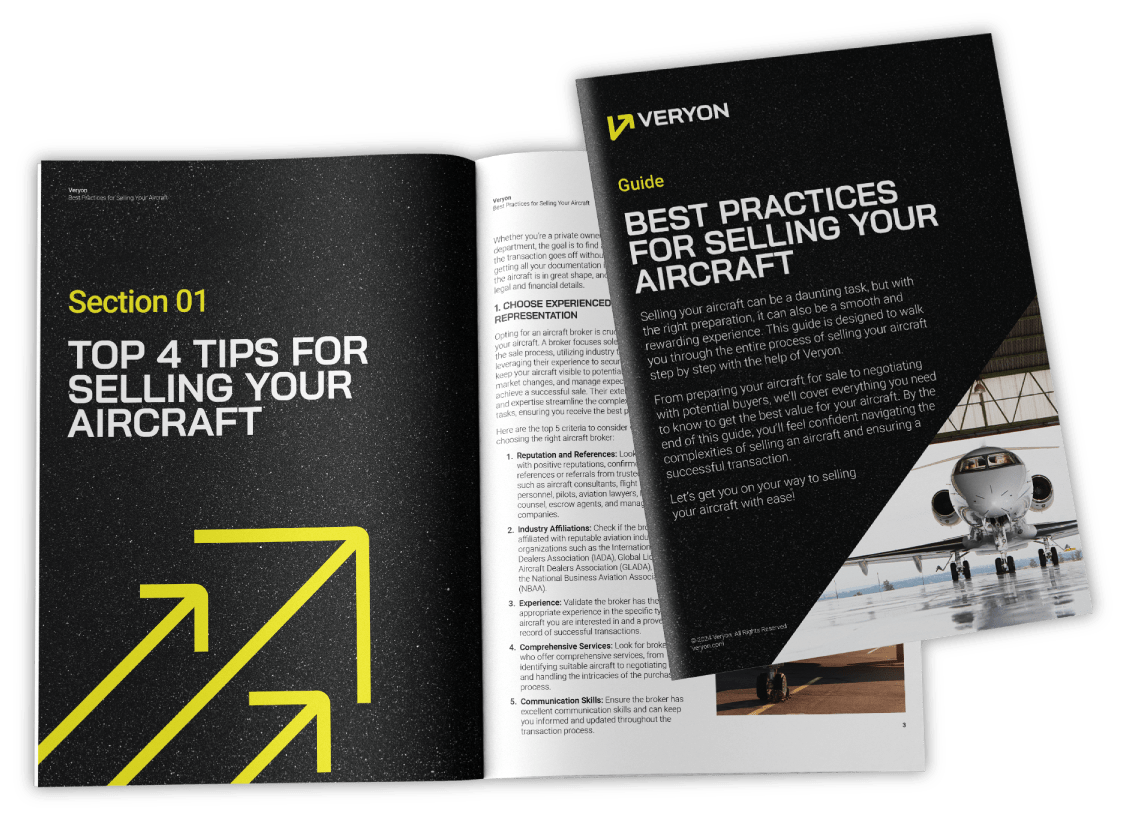
Kim Watne: "All maintenance records, including changes, part replacements, and major modifications, are crucial. Having complete and accurate data is essential."
Increased Aircraft Downtime
Myth: Aircraft downtime will increase during the transition.
Fear: Users worry that switching systems will disrupt operations and increase downtime, affecting flight schedules and aircraft availability.
Debunked: With proper planning, the transition can be managed without significant downtime. Often, the transition process can be aligned with scheduled maintenance or downtime periods, ensuring minimal impact on operations.
Conclusion
While transitioning to a new maintenance tracking system may seem daunting, the benefits far outweigh the challenges. Moving past the myths and embracing modern systems like Veryon Tracking offer significant improvements in data management, operational efficiency, and overall aircraft value, making it an indispensable tool in today's fast-paced industry. By overcoming the fear of change and embracing a more advanced, integrated platform, aviation companies can ensure their operations are compliant and optimized for growth and success. To schedule a demo, contact us today.