End-to-end solutions for Commercial aviation
Increase revenue hours, reduce maintenance turn-around times, and
facilitate cooperation between your engineering, maintenance,
supply chain, and flight ops teams.
Veryon provides a range of solutions for commercial operators that help overcome some of the industry's key challenges:
Tracking and proving regulatory compliance
Improving maintenance efficiency and effectiveness
Identifying areas of improvement from vast amounts of data
Ensuring part availability while keeping inventory costs low
You've got to get more uptime. And that means three things:
No more waiting.
Get everything you need right at your fingertips, including real-time visibility of maintenance data, operations data, regulatory data, and more.
No more wondering.
With an intuitive platform interface that makes it easier to find what you’re looking for, plus a team of experts with deep aviation knowledge.
No more wasted effort.
With an intelligent database that leverages AI and machine learning to simplify everything from documentation to troubleshooting.
Our solutions
Reliability
Predict and mitigate component failures, simplify compliance reporting, and enhance fleet reliability.
Guided troubleshooting
Interactive and collaborative troubleshooting while capturing new field experience.
Fleet management
Track airworthiness across your fleet and proactively plan maintenance.
Inventory management
Optimize inventory planning and easily procure or sell aircraft parts.
Business support
Manage your human resources, finances, and quality & safety functions.
Commercial airlines and operators all over the world depend on us
Veryon's solutions are currently used by 25% of the worldwide commercial fleet to manage aircraft and streamline maintenance.
After nearly 50 years in the business, we have built a growing reputation for getting our customers more aircraft uptime.
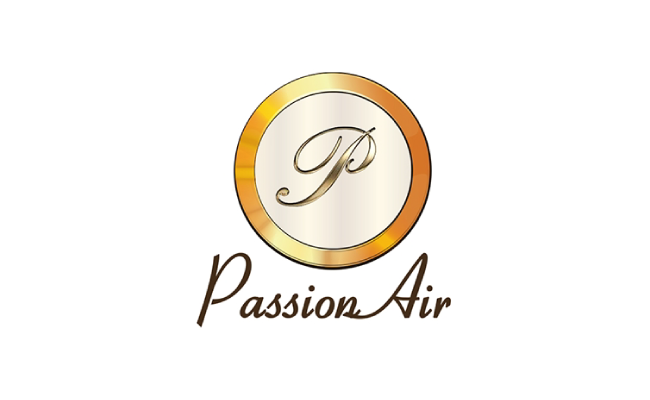
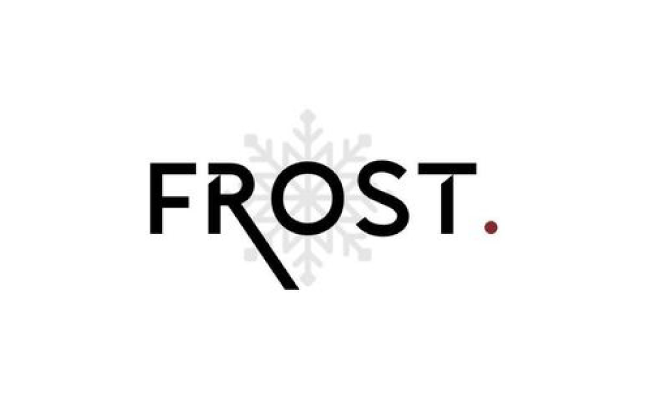
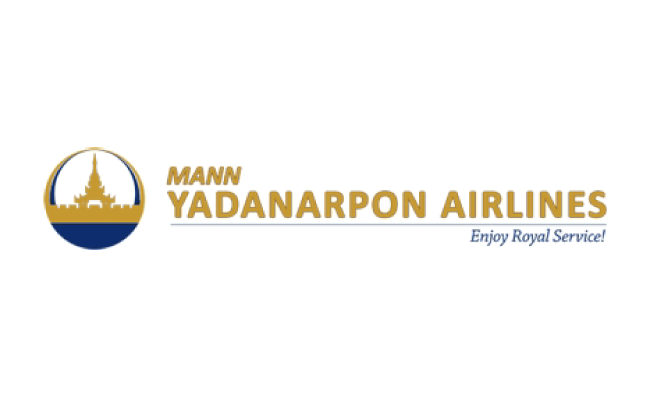
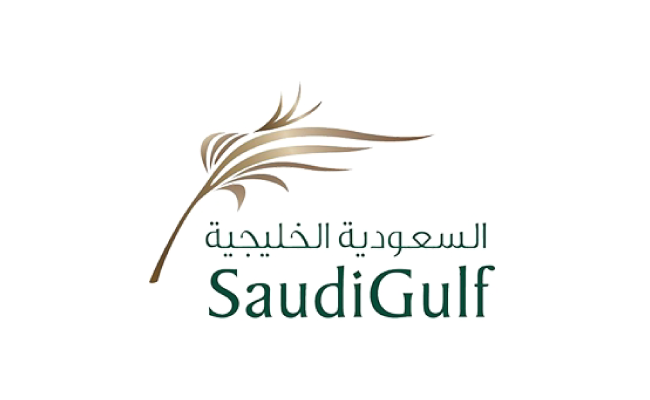
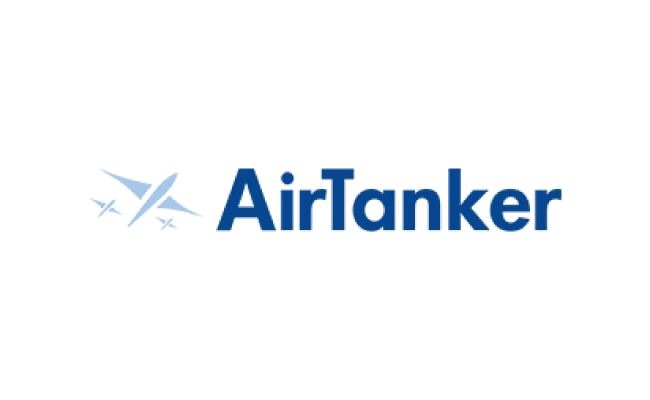
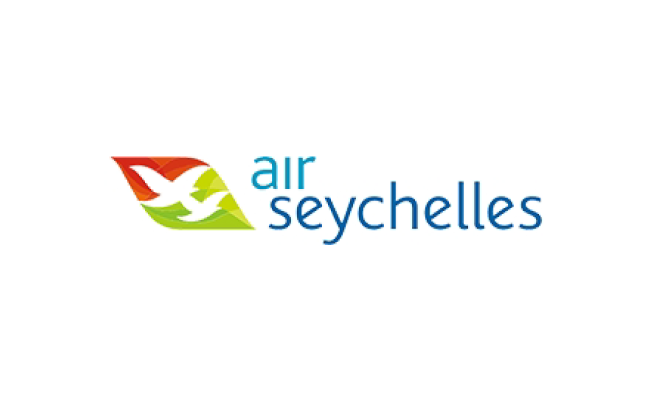
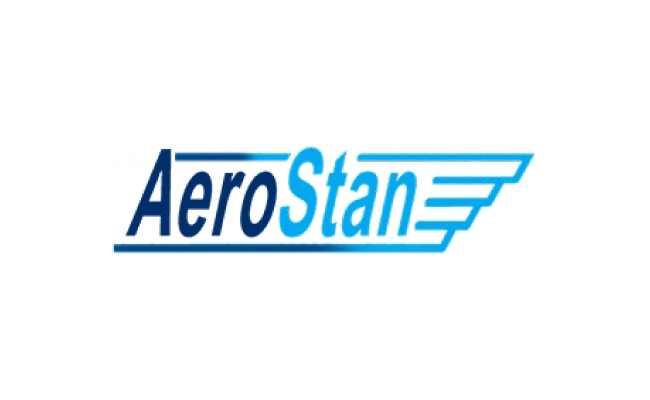
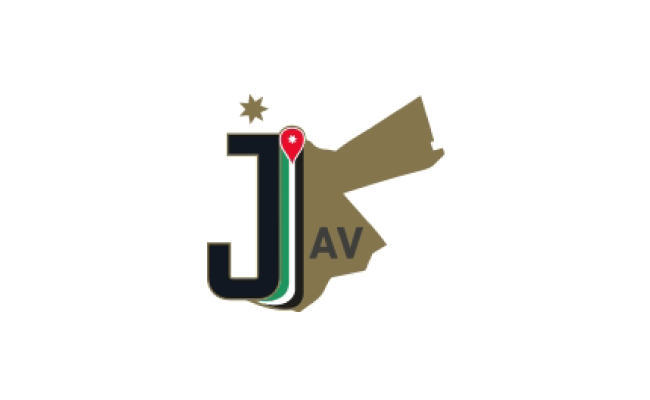
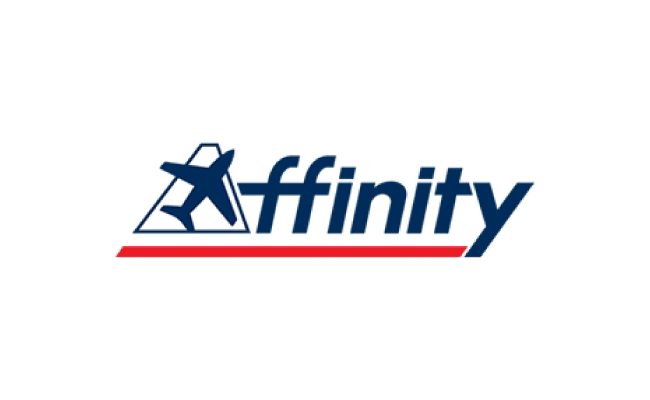
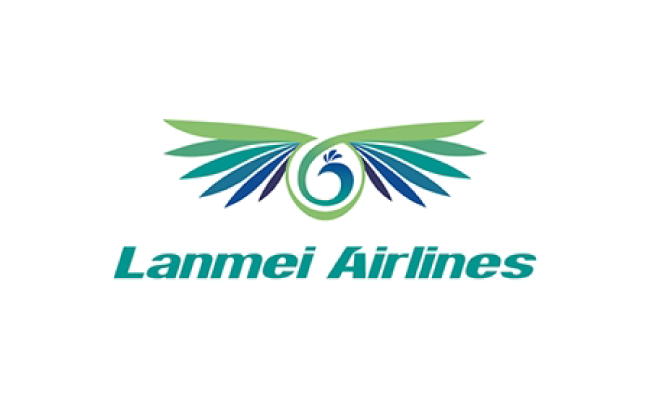
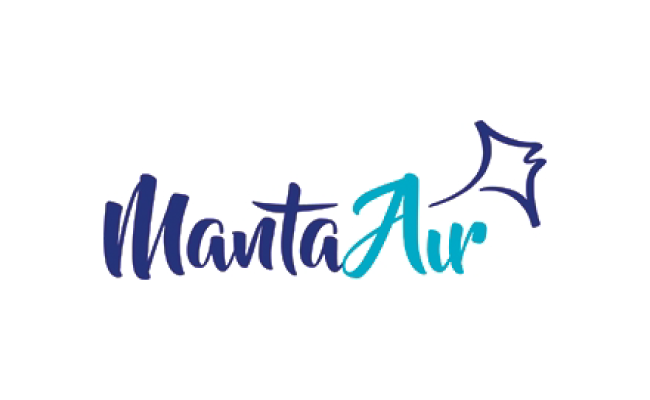
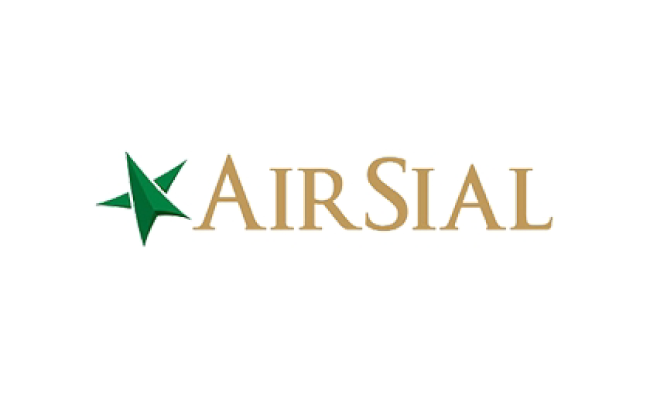
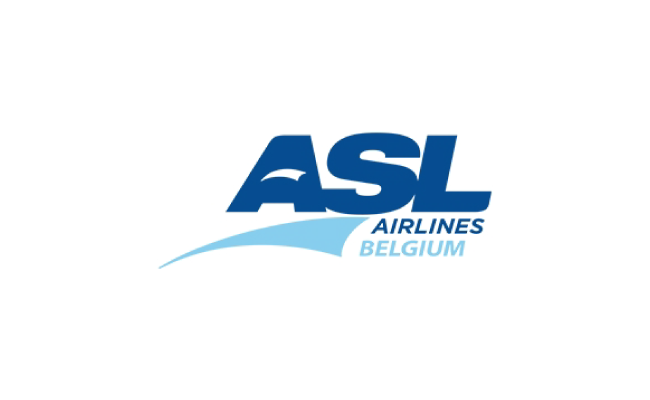
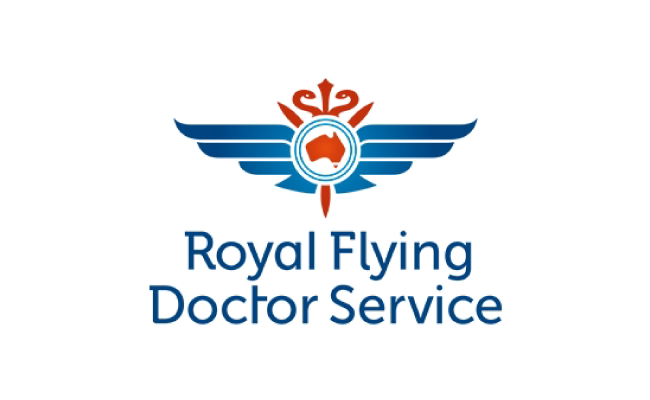
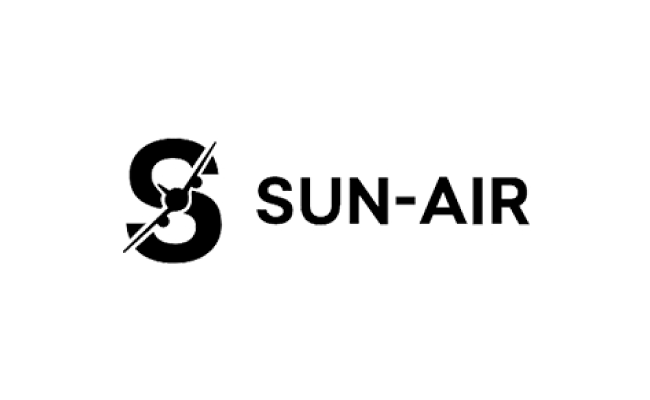
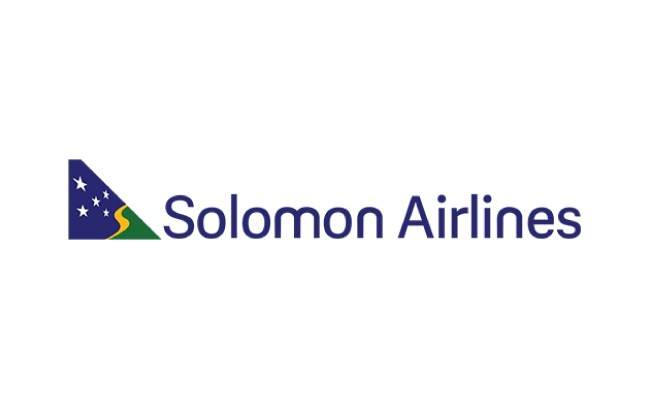
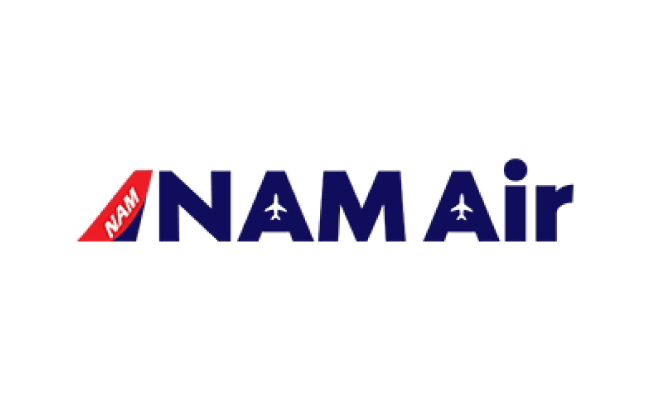
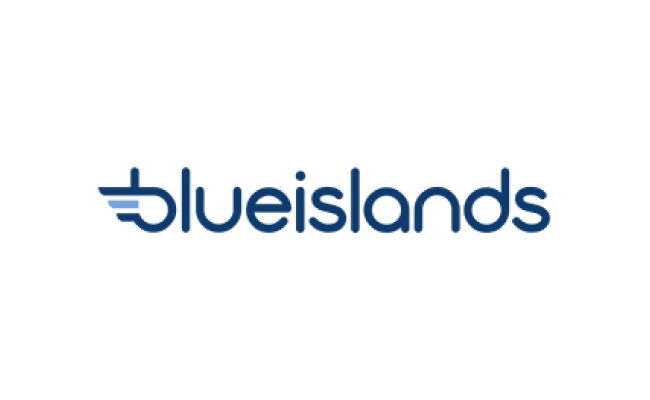
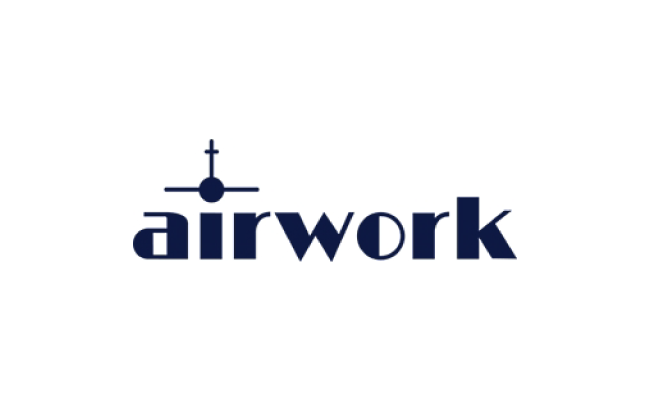
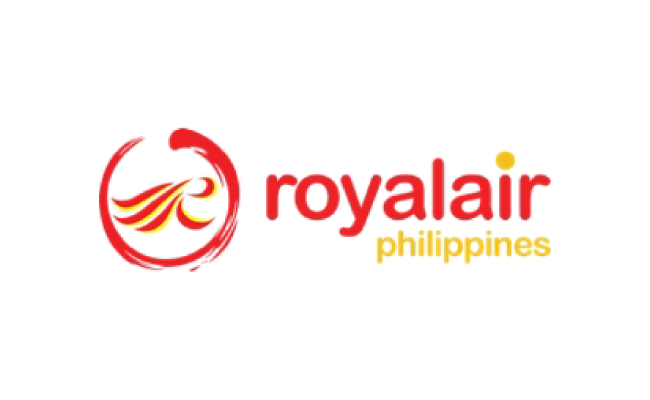
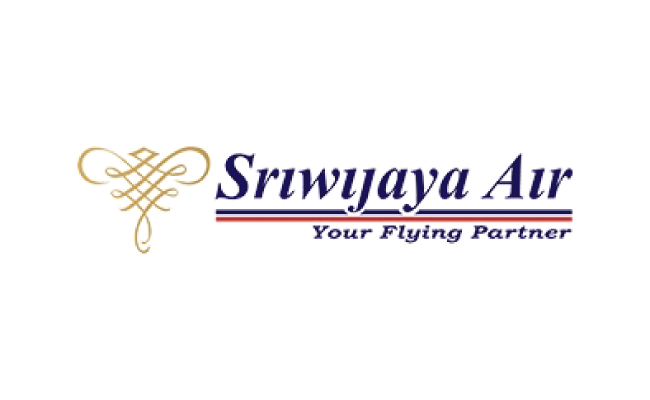
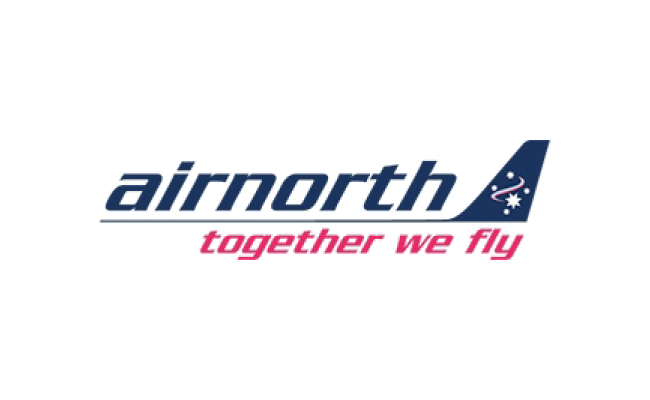
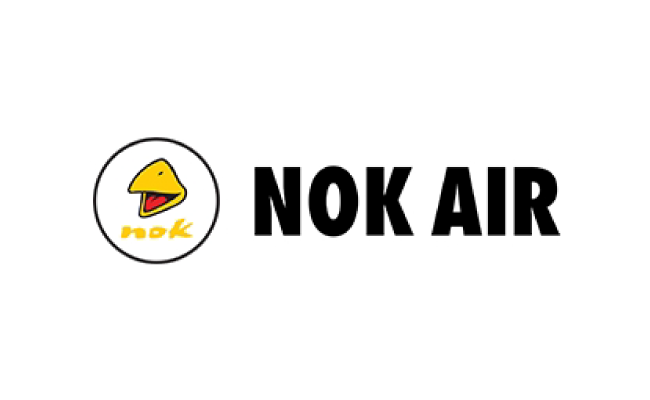
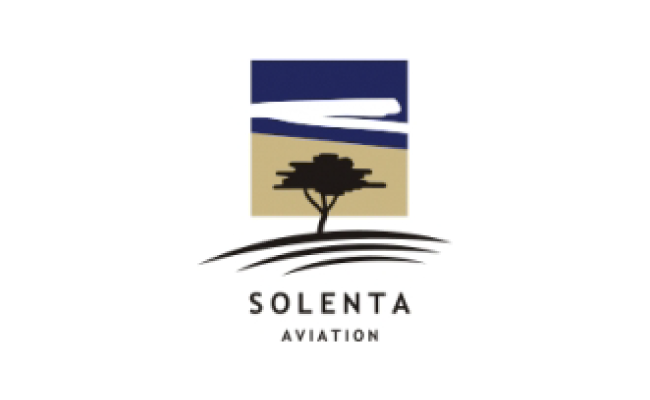
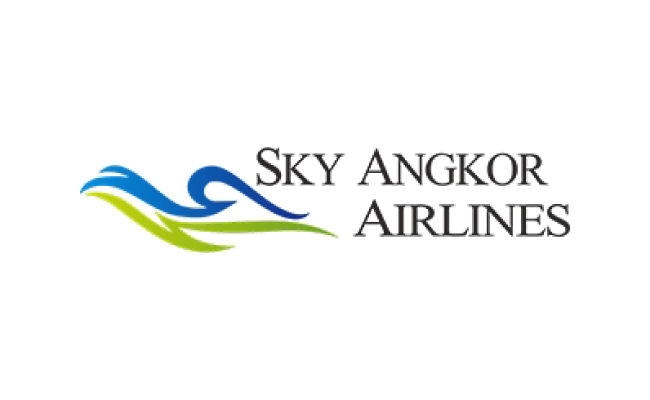
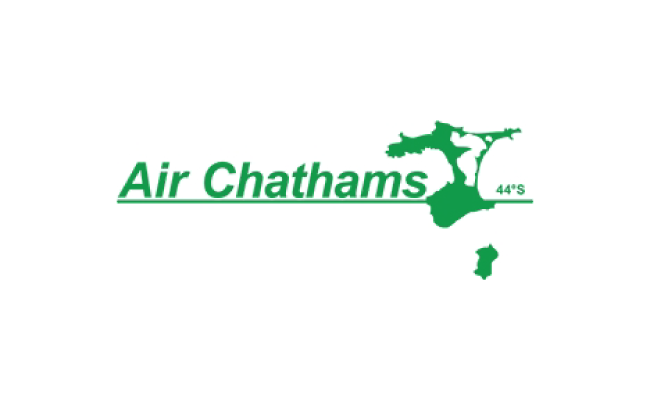
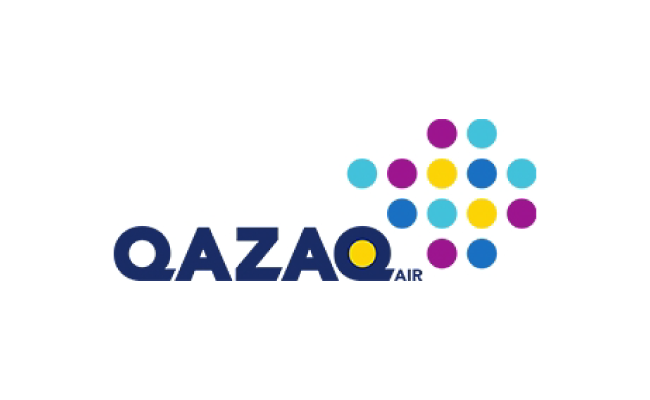
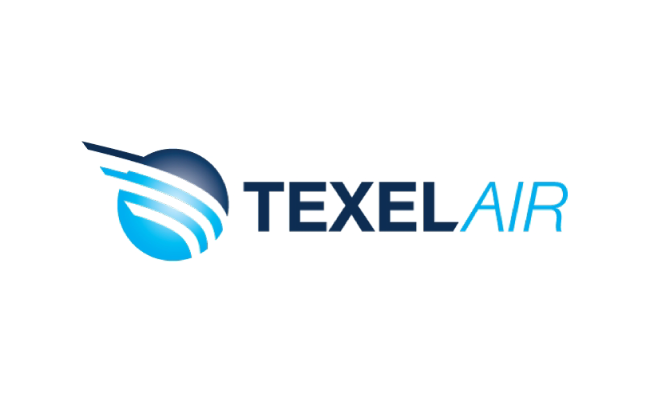
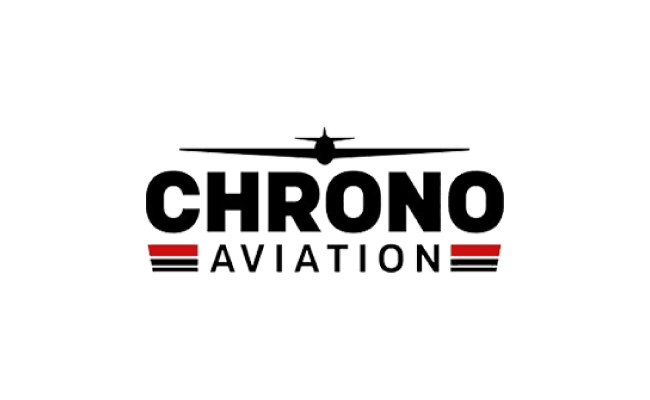
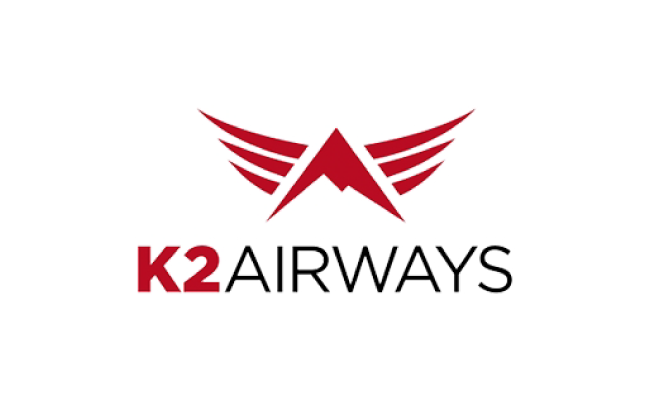
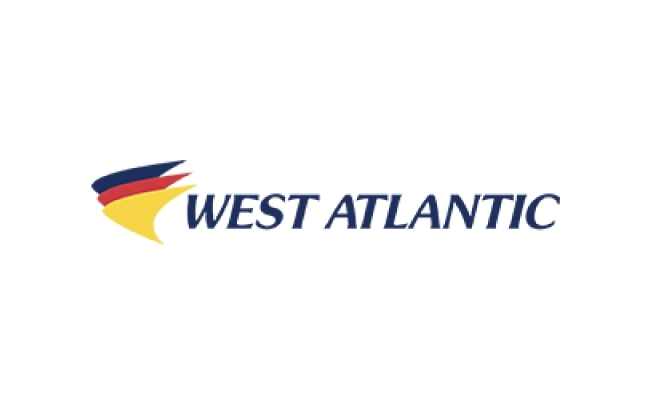

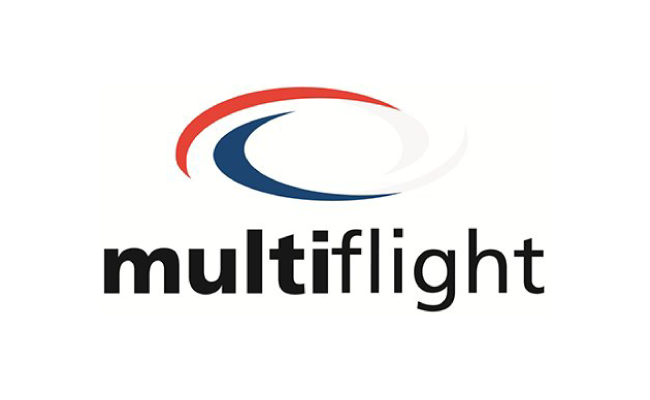
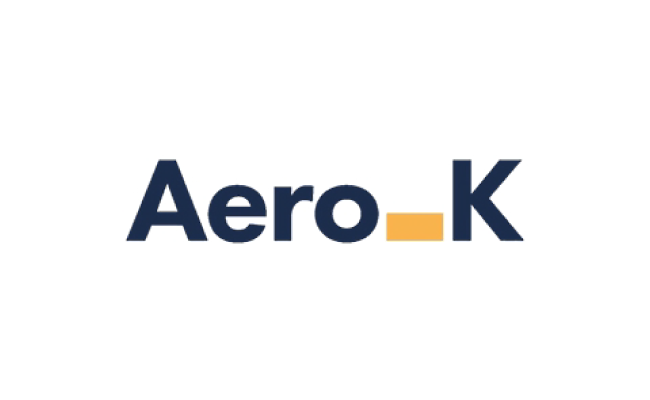
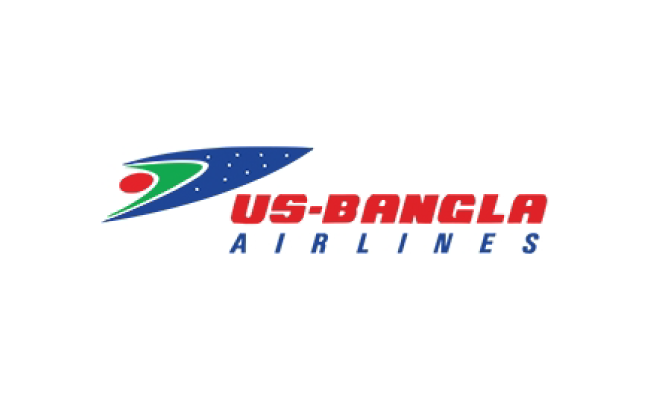
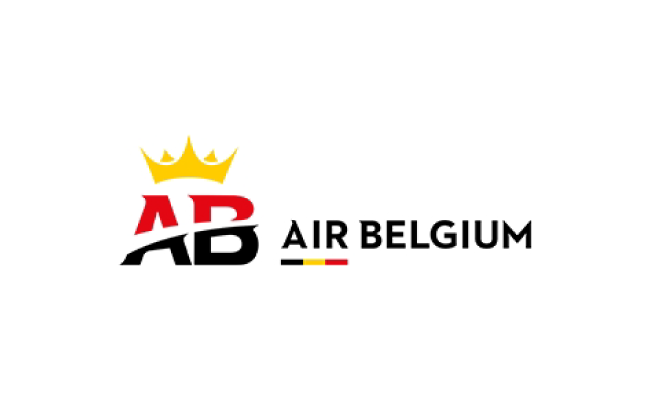
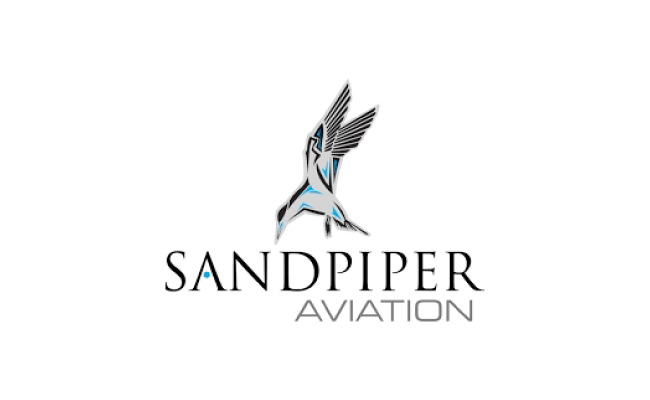
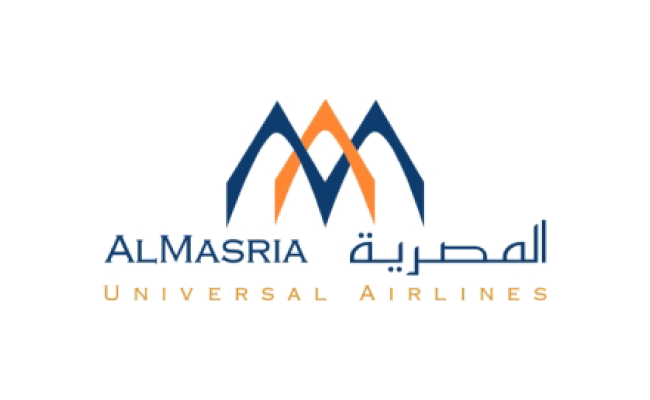
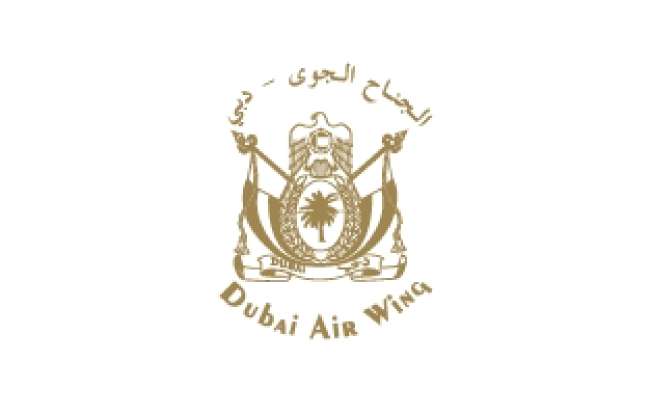
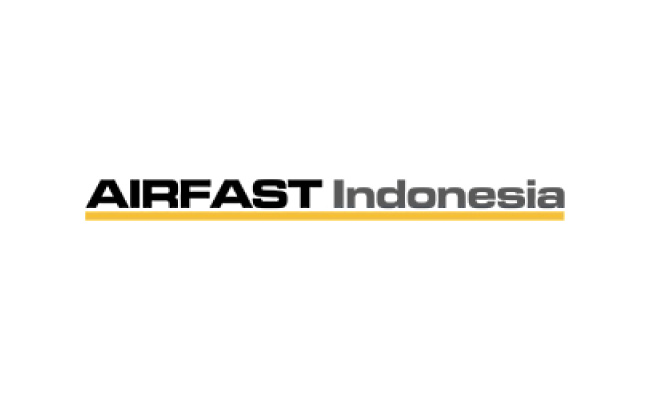
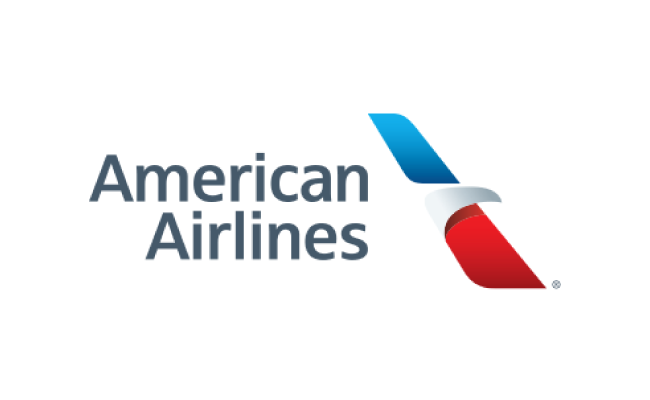
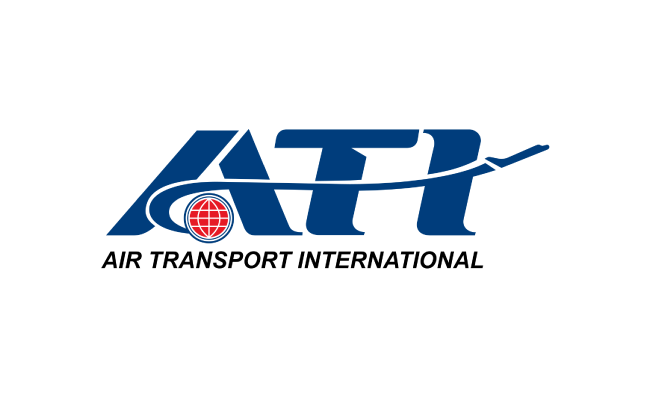
Hear what our commercial airline and operator customers are saying
"Prior to getting Veryon Defect Analysis, we would have to do a broad search of all write-ups, extract it into excel, filter it, try to find all the items tied to it and there could be hundreds of thousands of write-ups. When we got Veryon Defect Analysis, right away it was telling us “well here’s your write-ups that are all tied together.” It made it a lot simpler to see the history of what’s going on with it."
Manager of Maintenance Control
Regional Airline
"Veryon Defect Analysis is a more powerful tool than we’ve ever had before. It has improved our process on a daily basis."
Director of Maintenance, Operations Control
Major North American Airline
"We were very grateful for Veryon's support during the implementation, as it ensured a smooth and successful start to our operations."
Aero K
"We see Veryon as a key partner to our business rather than just another supplier. We look forward to working on more exciting projects with them in the future."
Airwork
"Veryon stood out for us because of its use of modern technologies, and its user-friendly interfaces."
Berry Aviation
"Tracking+ had all of the features and capabilities we were looking for in a solution and has helped overcome the challenges we were facing as a business.
Chrono Aviation
"It was very important for us to find a modern and technologically advanced solution that could foster a paperless environment for our operations."
Frost.
"Veryon has enabled us to consolidate our previous solutions and 3rd party services into a single, end-to-end platform, greatly improving our oversight and productivity."
Nok Air
"With Veryon Guided Troubleshooting, we can diagnose equipment problems 2-4X faster than with other methods, with almost no variation in elapsed time between rookies and experts."
Field Service Technician
Major OEM
"Veryon’s technology helps us gain greater visibility of our maintenance process and wider operation, giving us a truly end-to-end system."
Royal Flying Doctor Service
"Veryon Tracking+ allows us to manage key elements of our business from one solution and effectively plan our activities to keep costs at a minimum."
Sandpiper Aviation
"For us, Veryon Tracking+ stood out from the competition because it was easy-to-use whilst functionally rich at the same time."
Sriwijaya Air
"With its depth in functionality and easily accessible interfaces, we see Veryon Tracking+ as the backbone of our future digital journey."
Texel Air
"[Veryon Defect Analysis] found a tremendous amount more receptive items than we knew even existed. We were able to fix these items at a quicker pace and they never escalated into major operational problems in the aircraft."
Operations Manager, Maintenance Control Center
Major North American Airline
"With Veryon Defect Analysis we found that the tool has greatly improved our performance with accuracy with really more repetitive issues, efficiency, decreasing the time of identifying those issues, and overall the knowledge that the tool brings us."
Director of Maintenance, Operations Control
Major North American Airline
"Time savings, work flow, reliability are definitely keywords to use when talking about this service. With Veryon Defect Analysis, ATA miscoding is no longer an issue with the word search and data mining. We can now find chronics trends that span across 3 or 4 different ATAs."
Manager, Maintenance Operations and Control
Regional Airline
"Regulatory issues brought us to use the Veryon Defect Analysis program. After we started using it, it corrected all of the regulatory problems."
Operations Manager, Maintenance Control Center
Major North American Airline
"Seeing some of the issues when we do see them hit, we are a lot better at reacting and getting them routed in before they do become another delay or cancel down the line."
Manager of Maintenance Control
Regional Airline
"They were spending around 4 hours a day on our old program, and now they have cut that in half to around 2 hours. They are now working to find solutions rather than trying to find which items are repetitive."
Manager of Operations Maintenance Control
Major North American Airline
"By collecting and sharing best practices and field experiences, we provide an unprecedented level of diagnostic capability for operators."
Aircraft Maintenance Engineer
Airline