5 min read
Transforming Aircraft Maintenance Management: See Why Operators Are Choosing Veryon
Veryon : Aug 12, 2024 8:00:00 AM
Table of Contents
Choosing the right aviation software plays a crucial role in transforming aviation management, allowing seamless operations across the board. By leveraging the right platform, aircraft operators can enhance their efficiency, safety, and overall performance.
From flight planning and scheduling to maintenance tracking and crew management, the right software can consolidate processes, improve decision-making, and ultimately optimize operations in the aviation industry.
Additionally, using an integrated aviation management software platform allows customers to empower themselves daily, knowing they have the most advanced tools and the peace of mind that data is always secure and accessible.
Experiencing repetitive issues with aviation software is undoubtedly frustrating, especially in an industry where accuracy is paramount. Below, we've compiled the top pain points our customers have experienced with other software companies before switching to Veryon and how our robust platform and unmatched customer service address those issues.
Pain Point: Real-Time Access to Maintenance Status
A common frustration among aircraft maintenance teams is the inability to access real-time updates directly. As one Director of Aviation Maintenance for a Part 91 and Part 135 Operator pointed out, "We can't log in to CAMP and see our maintenance status. You have to send them an email and ask for a report."
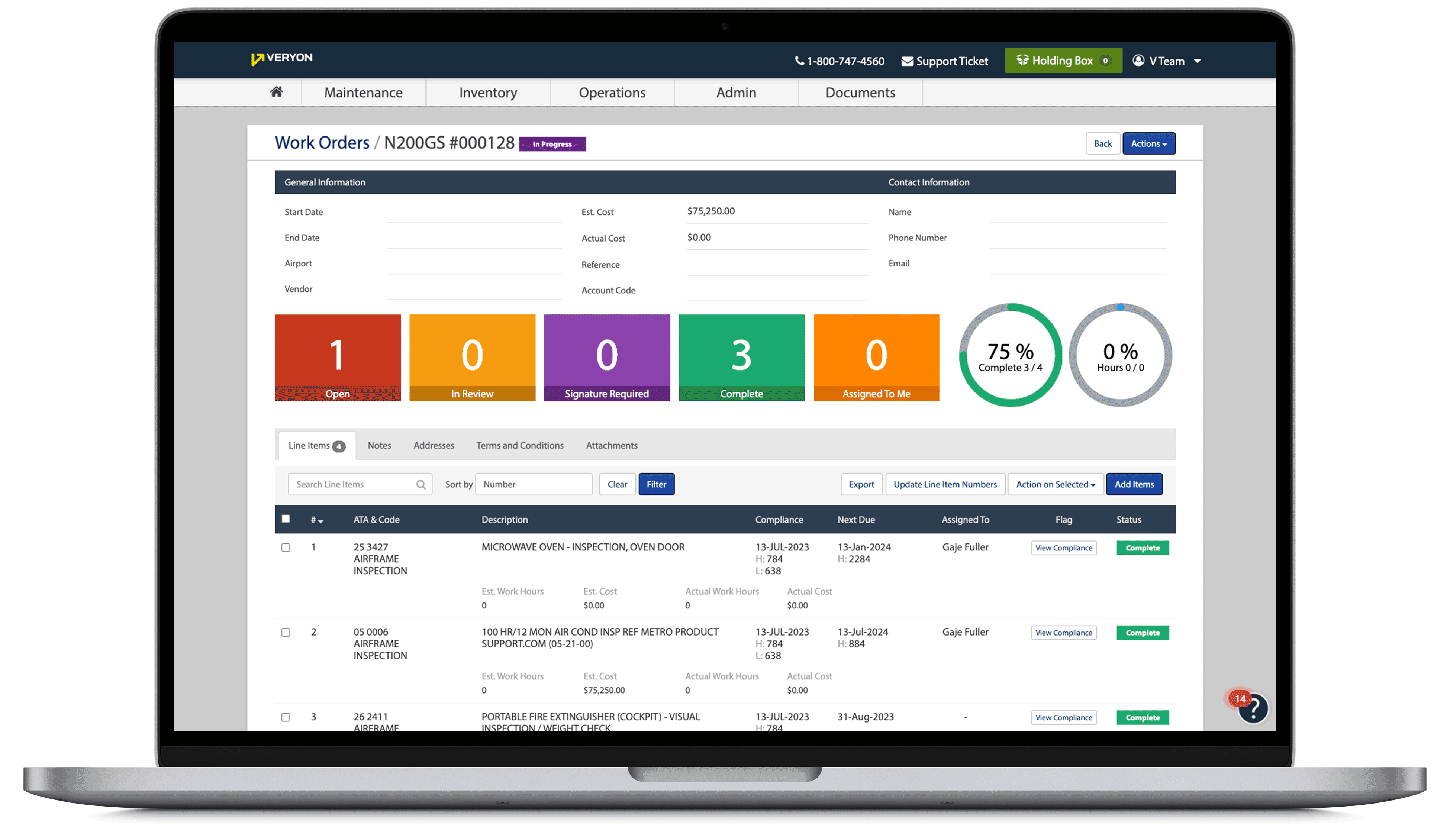
With Veryon Tracking, users are offered a calendar view with different statuses for each aircraft. Users can filter and view specific maintenance items and work cards. Maintenance items are populated based on the aircraft model and regulations, and initial enrollment requires digitized log copies.
The platform features eLogbooks for digitally creating and storing logbook entries, checklists for preflight checks, document uploads, and access to Veryon publications, and offers maintenance items list filtering. Users can filter the maintenance items list by date range or interval, use the search bar for specific descriptions, generate reports, and export them to PDF or Excel. They also can attach additional items, including pictures and videos, to task cards via the mobile app.
Users of CAMP have raised concerns about work order tracking and invoicing, particularly the process of creating work orders and billing for managed aircraft. As one Director of Maintenance for a Part 135 Operator describes:
"I have to print off the CAMP work order and manually add up all the time because their system doesn't calculate it correctly. The formulas just don't work, and since they own Corridor now, they won't spend any time or money fixing it. So, I print it out, add everything up with a pencil, and write down the total. They get the handwritten numbers and don't like it because they worry about human error. They always double-check it by adding it up themselves. If we had a computer program to do this, it would save the owner both time and money."
Veryon's Work Center allows for creating work orders, assigning users, tracking labor and parts, and generating invoices.
Work Center allows aircraft operators to simplify the maintenance and return-to-service process with streamlined invoicing, reliable integrations, and real-time airworthiness information — all in a unified platform. Aircraft operators can efficiently coordinate labor, parts, and operational impact, resulting in smooth maintenance execution without any unnecessary delays or disruptions.
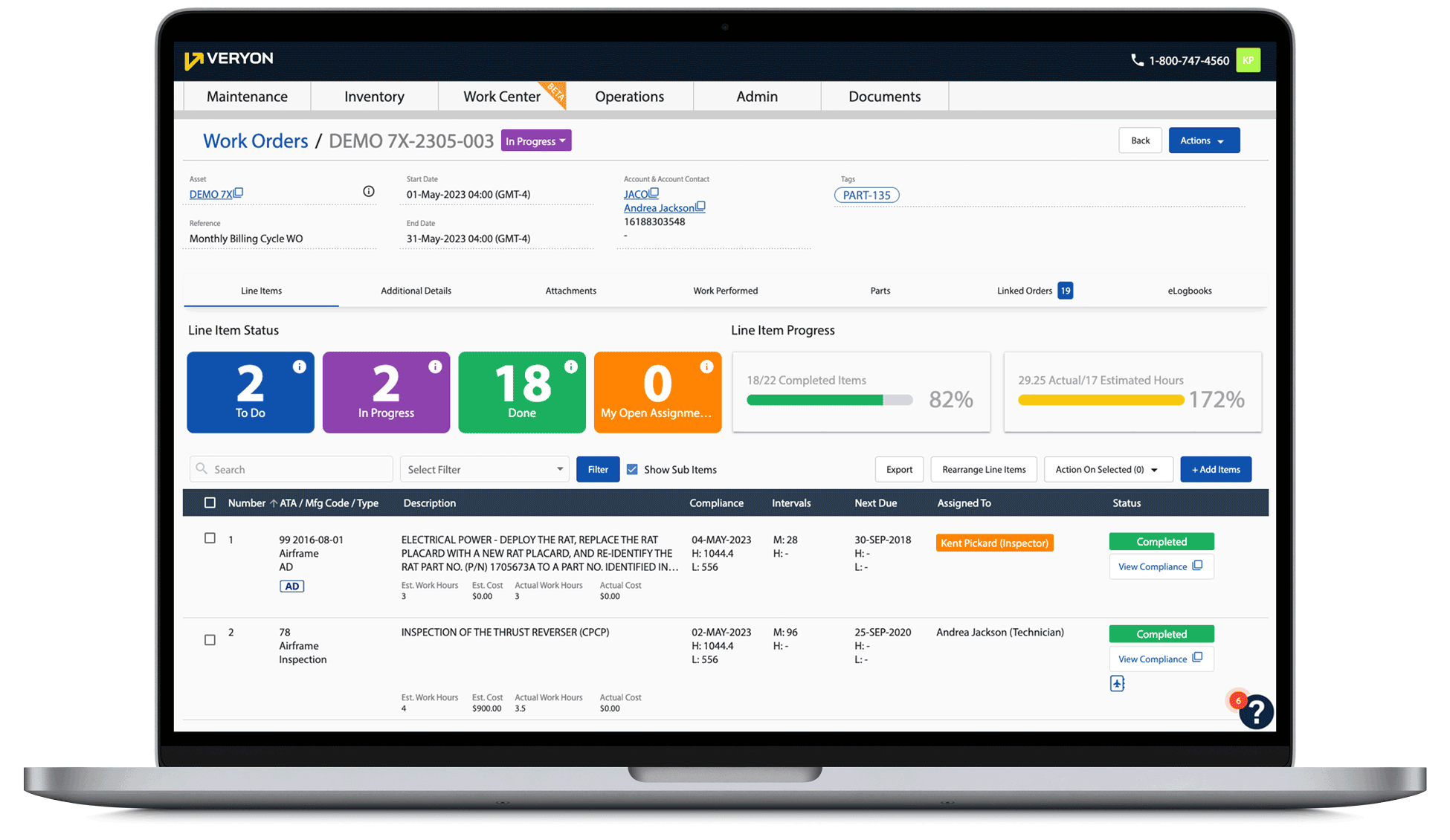
Users have experienced integration problems between maintenance and supply chains in CAMP that have led to inefficiencies and duplicated tasks. As one Supply Chain Specialist for a Part 135, Part 121 Operator explains:
"In CAMP, our main problem is that we cannot follow the chain between Maintenance and supply chain. There is no connection at all. When the technician creates a work order, he doesn't see if I took any action. His main wish is to have a clear view of all Maintenance procedures. The process should be easy and smooth."
Veryon Tracking integrates maintenance and supply chain information, enabling easy tracking of work orders, supply chain status, and communication. It also provides unlimited document storage and mobile access, monitors airworthiness directives (ADs) and service bulletins (SBs), and includes features like task assignment, parts tracking, and purchase order generation.
An added bonus? The system sends email notifications for new revisions or directives with backup documentation, and it allows for easy report generation, including to-do lists and maintenance item reports.
Users of other software solutions often struggle with inefficient processes and lack of integration between systems. This disconnect leads to increased costs and daily headaches. As one Director of Maintenance for a Part 135 Operator puts it:
"I’m looking for the best option because I have to work 24/7. When we send our aircraft for maintenance, they complete the logbook entry with the release to service and send us the documentation. Then, I had to start putting all our data into our old system task by task. If you have 72 tasks, then you are sitting there for two days."
Similarly, a Helicopter Maintenance Inspector for a Part 135 Operator points out:
“Our current software doesn't integrate into anything on the flight ops side. So, we have to manually provide technical dispatch for the aircraft, which is not ideal.”
To address these issues, it's crucial to have a comprehensive maintenance tracking system that seamlessly integrates flight operations and maintenance tasks. Veryon Tracking rises to this challenge. Unlike restrictive systems like CAMP, Veryon Tracking allows for full autonomy with easy compliance updates and integrates with all major flight scheduling platforms.
With Veryon Tracking, you can:
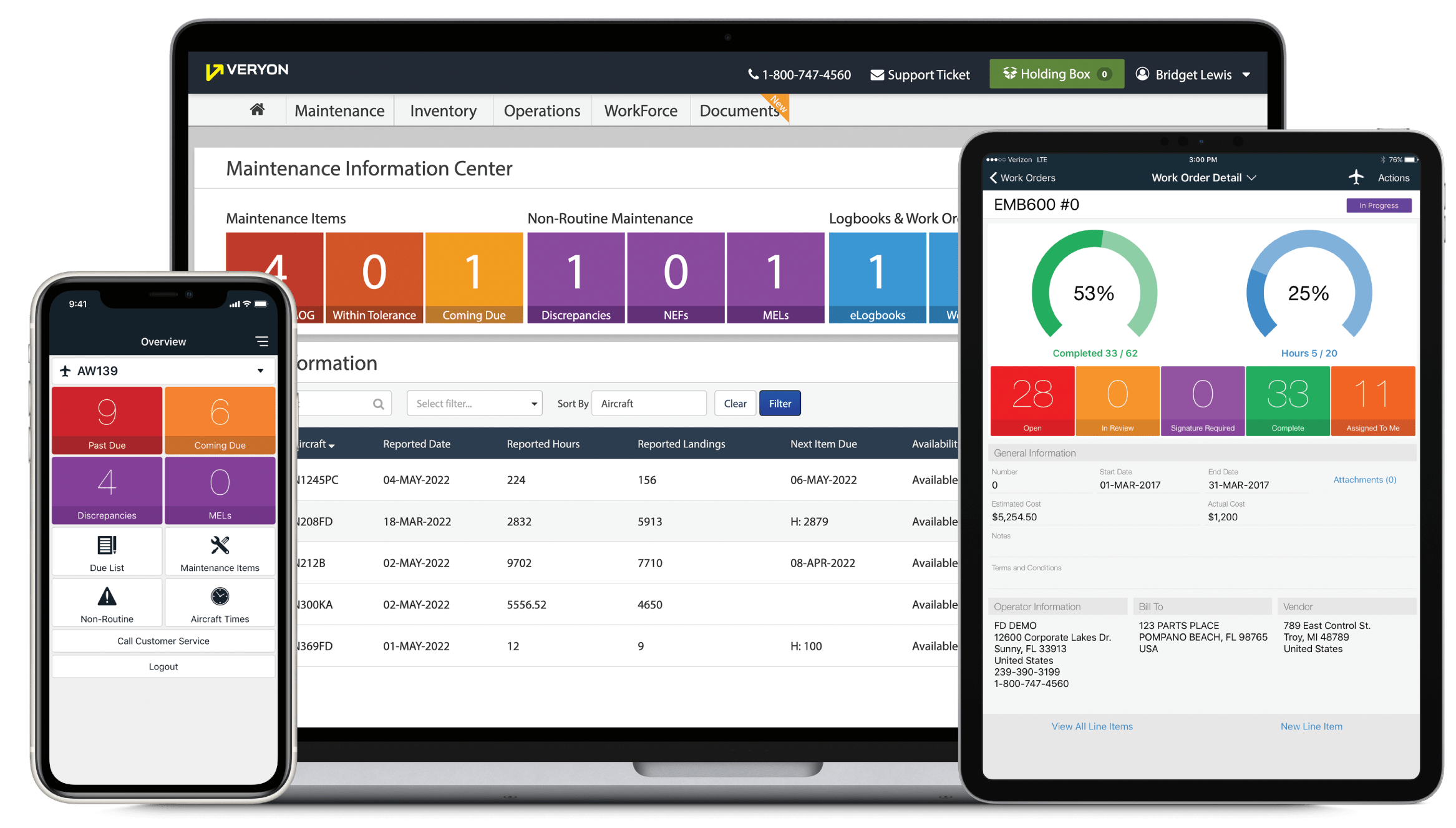
Track and manage your aircraft, fleet, and compliance at a glance.

Coordinate and optimize inventory management across departments.
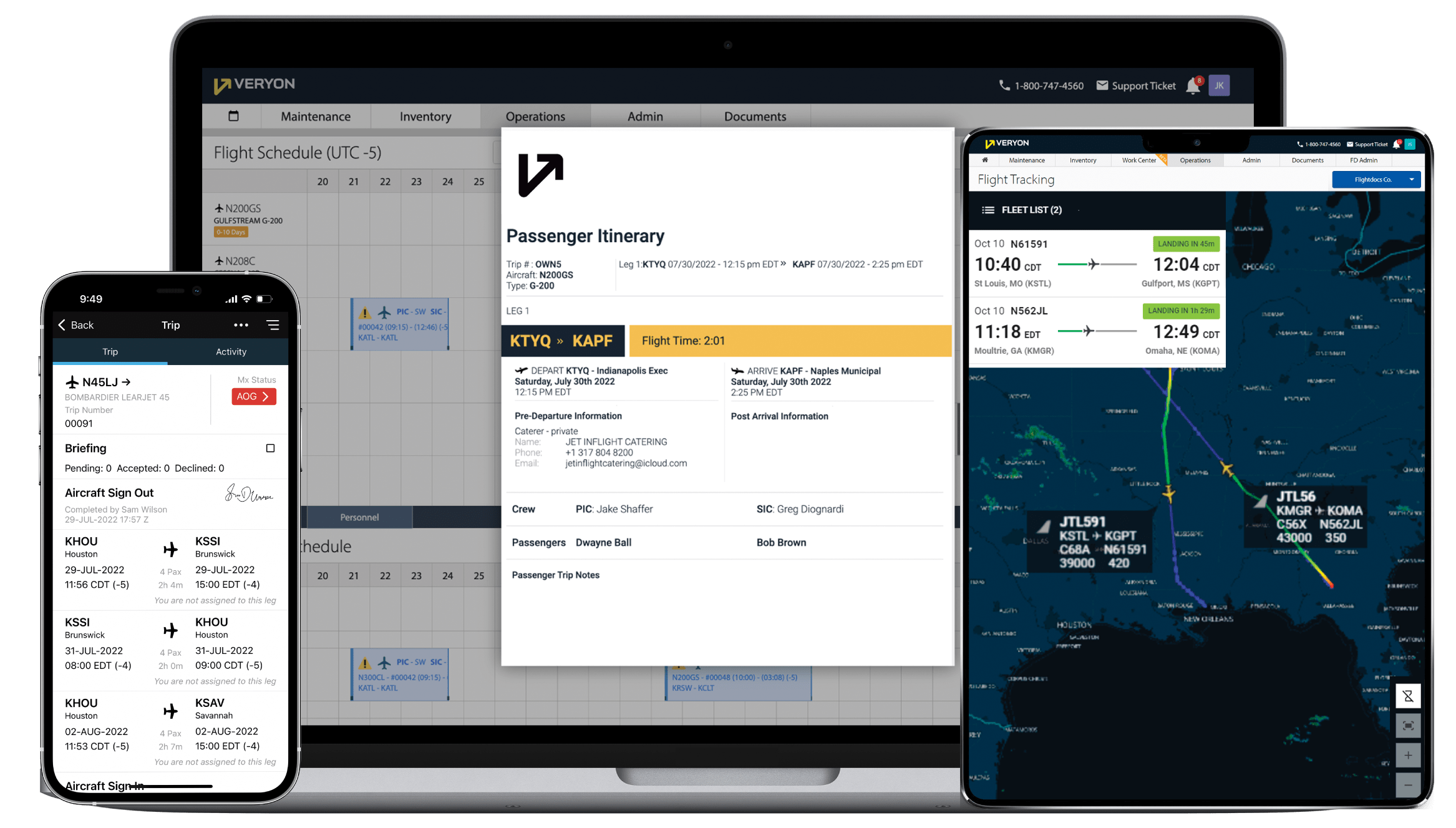
Create trips, manage crew, and communicate with team members in a single up-to-date calendar view.
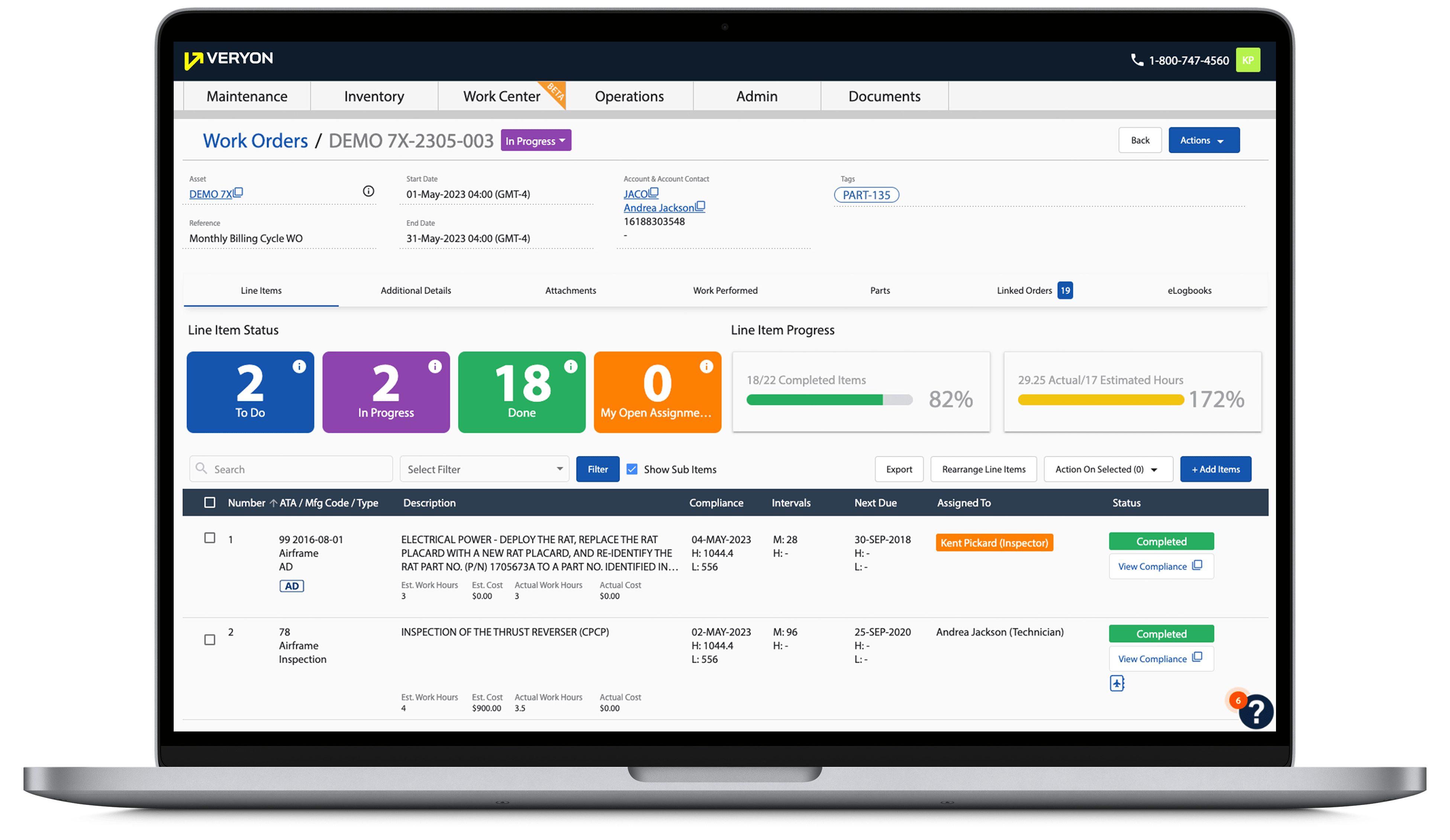
Expedite return-to-service with a unified platform that leverages the combined power of maintenance tracking, parts procurement, and invoicing.
Veryon Tracking also features an open-source API for smooth integration with other platforms, ensuring a more streamlined and efficient operation. One Part 135 operator highlights the benefits:
"The accessibility through the APIs is the biggest thing for us. We use a program called AirTable for our operations, and with Veryon's integrations, we've been able to link different data points seamlessly. For instance, we can see current aircraft availability by integrating Veryon's data into AirTable, producing a Tableau report. This integration doesn't add any extra work and provides maximum visibility across our organization."
Few things are more frustrating than needing an immediate answer only to find that your dedicated analyst is unavailable. As one Part 135 Operator providing charter services explains:
“Our flights typically operate from 8 a.m. to, let's say, 8 p.m. Our maintenance essentially starts around 8:30 p.m., and if you have to wait until your analyst responds to you from CAMP, it could be the difference of you missing an entire day of revenue.”
That’s why Veryon provides a team of analysts available 24/7, 365 days a year, ready to assist you at any time. Plus, you’ll have a Customer Success Manager, a resource and platform expert dedicated to your needs.
The Part 135 operator further elaborates on the benefits of responsive support:
“The 24/7/365 responsiveness provided by Veryon makes a significant difference for us. The accessibility of knowledgeable support staff around the clock has enabled us to promptly address any issues or concerns, minimizing downtime and maximizing productivity.”
Veryon also offers in-house technical records and data quality team comprised of aviation maintenance experts with experience, such as Directors of Quality, Directors of Maintenance, AMPs, and Analysts.
Locating files based on work orders can be cumbersome, particularly when establishing efficient practices for new aircraft. As a Maintenance Supervisor at an MRO operation points out:
“It’s Important to have all task cards linked in the history for clean records. Finding files based on work orders is ridiculous, and we want to start off right with a brand-new aircraft.”
Veryon tackles this challenge head-on with its advanced features designed to streamline task card management and historical record-keeping, including:
-
Task Card Linking and History
Veryon updates records and applies task cards based on the information provided. Customers can input data from a memory stick into the system or have Veryon’s team of analysts apply task cards and update records. -
Compliance Feature
On the maintenance items page, users can update times and add work descriptions. Technicians can electronically sign off on return-to-service statements, which are then logged in the system's digital logbook. Users can also manage personnel by adding license and certification numbers. -
Attaching 8130s to Tasks
Customers can send 8130 forms to the Veryon team, who will attach them directly to the relevant item or store them securely in the document repository.
Conclusion
Transforming the way you manage maintenance requires more than just adopting new software—it involves selecting a platform that genuinely addresses key pain points and enhances operational efficiency. With an all-in-one aircraft maintenance management platform, you get advanced features that simplify your tasks and keep your data secure and accessible.
By choosing Veryon, you’re not just upgrading your software—you’re giving your team the tools they need for a more streamlined and cost-effective operation. To receive a free demo, contact our team today!